A number of times on the show it has been mentioned that an exhaust system without back pressure can lead to burned valves, notably the exhaust valve. I’ve talked to a few friends with auto experience and they agree this is the situation. However, this seems counterintuitive, and none of us can fully understand or appreciate what’s happening. Can someone out there explain the dynamics of this, and then in turn tell me the techniques used by racing vehicles to avoid this problem with their open exhaust systems. TIA, Brian
I’ve heard that too, and even the more extreme claim, that running an engine without the exhaust manifold will cause complete valve failure (I think the mechanic at the gas station where I worked said something like ‘it’ll make the engine suck the valve’, whatever that means…). I don’t get it, either.
Exhaust gas has very little oxygen in it compared to fresh air: ~1% vs 20%.
It takes oxygen to burn metal.
If a leaky or too-short exhaust pipe lets fresh air reach the exhaust valve it burns.
The exhaust does not come out of the engine in a steady stream, it comes out in pulses.
This is pretty obvious with a single cylinder engine, like on a lawnmower.
When the exhaust valve starts to open the pressure in the cylinder is still pretty high.
So the exhaust gasses leave rapidly early in the exhaust stroke.
This creates a wave that travels down the exhaust path at the speed of sound: 1100 ft/sec.
Also, when a pressure wave traveling in a pipe reaches the open end (or a chamber, like a cat converter or resonator) a rarefaction (negative pressure) wave is created and travels back in the other direction.
At low engine speeds these waves can travel up and down the exhaust system several times on each stroke.
So exhaust gas can flow ‘the wrong way’ at times.
Good explanation, now I get it.
First, most racing engines are rebuild frequently. In the case of drag racing, after several runs (less than 10) the motors of highly sponsored teams get rebuilt. Therefore some valve burning is expected. The valves and heads are specifically designed and treated to tolerate conditions that would burn up a conventional valve in a street car.
You get back pressure at the exhaust manifold. There are sophisticated CAD/CAM programs for designing intake and exhaust manifolds. Back pressure in the exhaust keeps the newly charged unburned fuel from moving through the cylinder into the exhaust system. In racing engines some raw gas in the exhaust is OK as it makes for a more powerful engine and you’ll see flames coming out of the exhaust. There are no pollution controls on these motors. They are tuned for power.
Street cars have all kinds of anti-pollution requirements and drivers don’t want to do valve jobs every few weeks or months. Designing in some back pressure is just one aspect of building the motor to last, get good power, and not pollute beyond legal limits for the life of the car.
I don’t necessarily agree that lack of back pressure will burn exhaust valves. If that were the case many an airplane would have fallen out of the sky due to short exhaust stubs.
In fact, one of the methods of IDing an aircraft at night during wartime was to note the exhaust flame patterns.
Running short, unbaffled exhaust pipes on motorcycles also do not cause a problem.
Since this is not a problem with inherently hotter running air-cooled engines it should not be a problem on liquid cooled automobile engines. This is proven by the guys who run modded cars on the street with a straight exhaust; as in no mufflers or converters. A friend of my son ran his Mustang 5.0 like that for years with no problem.
I’d say if someone is burning valves they have a mechanical lifter holding an exhaust valve open a half-thousandth of an inch, they’re running too lean, or something to that effect.
It does make sense in the ‘no exhaust manifold or pipes’ case. But once any length of pipe is in place, I agree, then I don’t see it.
It has appeared to me that an open exhaust first and foremost causes a significant loss of low and mid range torque but when the engine is operated at wide open throttle under load and suddenly the throttle is closed, cold air is gulped back and will often warp a valve. Warping leaves a gap at the seat and when the throttle is re-opened the hot exhaust leaking through the gap burns the valve and seat.
On street car you very rarely see burned valves anymore. I drove my Bronco for well over 150k miles with straight pipes, no cats, no mufflers, didn’t burn a valve or anything. My brother drove an F-150 with a similar exhaust for over 100k miles, and again no burned valves. It may have been more commonplace in the 50’s and 60’s but these days you just don’t see it.
The valve warping explanation makes more sense than the first lines of my last post re. oxygen.
Otherwise the Overrun Fuel Cutoff would be a problem.
When the engine is above idle speed and the throttle is closed no fuel is injected or burned, so more oxygen goes through into the exhaust.
At any rate fresh air reaching the exhaust valve is bad news.
“But once any length of pipe is in place…I don’t see it”
The open end of the pipe (or a leak near the valve) can suck in fresh air when a rarefaction wave reaches it.
The gas in the exhaust pipe can move back and forth in both directions even though there’s a net flow outward.
Kind of like a organ pipe.
So the air could make its way back a few inches to the exhaust valve.
A leak between the exhaust manifold and head is sure close enough, and maybe the outlet of the manifold if it’s compact.
Probably happens more at certain engine speeds.
“I drove my Bronco for well over 150k miles with straight pipes, no cats, no mufflers, didn’t burn a valve or anything”
Pipes ran to the back of the truck? That’s well over 10 feet.
No way air makes it that far up the pipe.
I guess airplane engines can get away with short stubs because they run at a steady high output.
I used to hear this theory about the burned valves and took it as truth without ever thinking i through. Now I’m not so sure. I think a lot might depend on other factors.
Cars with open pipes seem to burn valves, but cars with open pipes also have other modifications intended to force more fuel into the chambers. Superchargers or turbochargers supported by larger injectors and modified mapping of the ECU to keep them open longer create a situation wherein still-burning fuel is pumped out the exhaust valves, even if the heads haven’t larger valves and the ports haven’t been been opened up to prevent restriction. If the latter mods have been sone it blows burning fuel through to the extent that when they’re run hard you can see the flames blowing out (if zoomies are the only pipes). A stock engine with open pipes still should have pretty much expended the hydrocarbons before the exhaust valve opens.
With old carburated engines there was still unspent fuel at the bottom of the power stroke and removing exhaust restriction and blowing the still burning fuel out the valve unrestricted could manifest itself as burned valves, but I’m not so sure that’s true with a modern engine.
I remain open to the arguments from both sides on this issue.
Circuitsmith gave a pretty good answer. Changing exhaust back pressure can change the overall fuel mixture in carbureted engines…If you are talking about taking the muffler(s) off a modern fuel injected engine with a converter and two oxygen sensors ahead of the muffler, then it will not make any difference except in noise level. The forward oxygen sensor will keep tabs of the fuel mixture and adjust it as needed to keep exhaust gas temperature in the safe range…(a lean mixture will burn very hot).
Racing engines usually use a tuned exhaust system, which utilize headers and a megaphone to aid exhaust gas extraction. With these parts in place, the fuel mixture is carefully set on a dyno for optimum performance and to avoid burned valves…
Harley owners who routinely remove their mufflers usually must have their carburetors re-jetted to compensate for the change…Harley shops, who have done thousands of these removals have become expert at selecting the proper jets and installing them…
I rode a number of motorcycles for many years with nothing more than drag pipes on them and never even saw a warped valve much less a burnt one.
Adjusting the carburetor on a '65 and earlier Harley could be done while tooling down the road at highway speed.
For many years belt and electrically operated air pumps have been feeding cold fresh air directly into the exhaust system; a.k.a. secondary air pump system.
The P-51 Mustang engines did pretty well at 30k feet in -30 temperatures with no more than an exhaust stub.
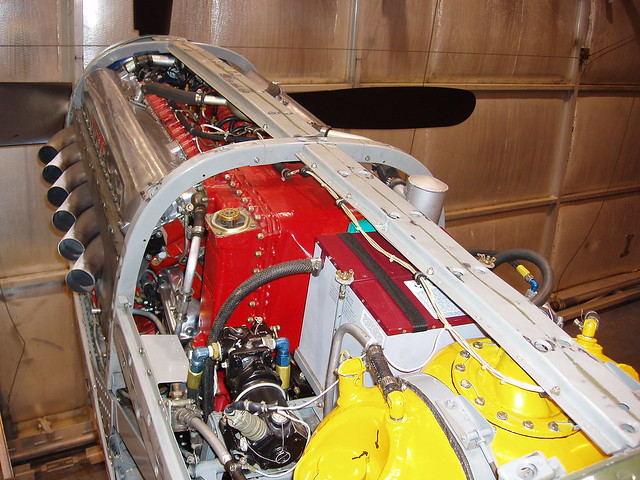
As a fellow mechanic, it is true you could toast a valve, although it has never happened to me. I’ve built race car engines and ran them with open headers and never had a problem. So I could not believe it when you told the Volvo girl that driving for three months without a muffler burned out the valves and caused her to lose compression, when, in reality, instead of forty or fifty thousand miles, it was probably one hundred fifty thousand miles on the car. When she ran up to 75 in 2nd gear, it stretched the timing components, and they failed when she shut off the car, a classic scenario for them to fail.
Many WWI aero engines, notably the Gnome Rotary and the LeRhone Rotary engines had no exhaust stubs whatsoever and were purposely timed so that fresh air was sucked back into the exhaust during the intake stroke. The intake mixture had to be extra rich to compensate for the exhast suckback leaning and it resulted in an engine that was unthrottleable, the power was controlled by switching the engine off intermittently with a kill button on the joystick for landing and taxiing.
This was done to help keep the exhaust valves cool back in a day when available exhaust valve metallurgy resulted in engines that had a TBO of tens of hours.
I never found the “an engine needs backpressure to make low rpm torque” theory plausible. I think what really happens in a straight pipe is that strong standing waves form that interfere with engine breathing at certain rpms and muffling the exhaust dampens those standing waves.
I tested the premise of this theory by using a 6 ft length of PVC pipe as a bugle. There are only certain notes that can be played and it was almost impossible to bend the notes up or down even a little. Then I drilled a bunch of tiny little holes on the last foot of the pipe so that the pipe no longer had a well defined ending point and it still strongly favored certain notes but now I could pull the notes up or down a little.
Car engines are starting to be designed to use intelligent variable valve timing to scavange (retain?) a bit of the exhaust gas when under load in lieu of EGR systems. The times they are a-changin’.
Let’s try to find some truth. With less backpressure, the hot gases can shoot out faster and could blow more metal off the exhaust valve. You have to know that metal gets blown off at a certain rate and if the velocity of the “torch effect” is increased, the metal blows off faster than normal.
If it didn’t, no valves would ever be burned. If you see a lot of burned valves, you see some of them looking like a slot was cut in the face by a hacksaw. They look like a blow torch was used on them.
Then there is racing with an open exhaust. Most of those engines are completely trashed when the race day is done.
The greater the back pressure the greater the amount exhaust gas that remains in the cylinder at the end of the exhaust cycle. The residual exhaust gas does two things. It reduces the amount of fuel-air mixture that can enter the cylinder. More importantly it heats the incoming fuel-air mixture reducing its density (less air less oxygen). Note: Changing the fuel-air mixture temperature affects the density of the air more than the density of the atomized fuel. With no adjustments to the fuel-air ratio remove the back pressure. The cylinder will fill more completely with a cooler denser (more oxygen) fuel-air mixture. The mixture will be ‘lean’. This will result in small performance increase due to increased cylinder filling. The problem: If the fuel-air ratio isn’t increased there will be excess oxygen in the exhaust gas. (The combustion flame becomes oxidizing) The big ifs. If the mixture is lean enough and if the valve temperature is high enough the excess oxygen in the exhaust will react with the carbon in the valve. It will burn. (Yes, similar to a cutting torch)
The answer is to increase the fuel-air ratio.
Thanks to everyone that chimed in on this discussion. It’s much easier to see now that there are multiple factors at play here with each/all doing their part to create a situation ripe for trouble if tinkering with a regular production vehicle, particularly if it has a lot of miles on it. My hat’s off to all.
Cylinder head valves that are badly burned are ruined because of a mechanical valve lifter being out of adjustment or a poor valve face/valve seat fit, not because of a backpressure issue.